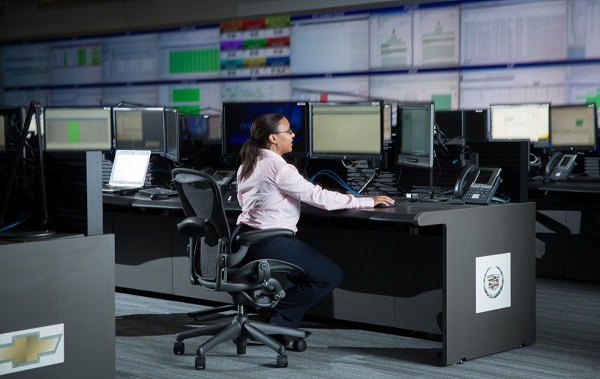
GM Ditches UPS for Flywheel; Shrinks 23 Datacenters to Two
[caption id="attachment_12407" align="aligncenter" width="600"]
Network operator Adrienne Johnson on duty in the data operations center of GM's new Warren, Mich. datacenter.[/caption] Power-saving in-row cooling and a flywheel that provides backup power without batteries are two of the improvements that made General Motors' newest datacenter 70 percent more power efficient than the list of datacenters it will replace. GM's Enterprise Data Center got a gold LEED certification from the U.S. Green Building Council, a certification given to fewer than 5 percent of U.S. datacenters, according to a Sept. 13 announcement from the company. The $130 million, 160,000-square-foot Enterprise Data Center in Warren, Mich., outside of Detroit, is one of two high-capacity datacenters the company is building to replace a global network of 23 data-processing facilities containing a total of 5 million square feet of computing space. The facilities bring control of all GM's datacenter assets back in-house, giving it better control over quality, availability and cost, as well as the opportunity to build the most energy-conserving technologies it could, according to Randy Mott, GM senior vice president and CIO, in GM's announcement of the award. Among the unusual choices was the decision to avoid the use of battery-driven Uninterruptible Power Supply (UPS) systems, which use the equivalent of 12,000 car batteries; instead, the company installed a flywheel system and a pair of 5,800-horsepower diesel generators able to produce 3 megawatts of electricity for backup power. The whole system is based on the Law of Conservation of Mass and Energy, but the principles behind its design and operation are largely the same as those behind a potter's wheel or grinding wheel in a flour mill. The more energy is pumped into the system, the faster the wheel spins and more energy it holds... as long as there is enough supplemental energy to keep it spinning at the same rate. Modern flywheels are typically carbon-fiber rotors suspended by magnetic bearings, rotating in a vacuum chamber to reduce friction. Friction-eliminating design elements, high rotational rates and the use of higher-voltage exchanges than those used by battery driven backup systems – which make it possible to eliminate transformers that bleed out a certain amount of energy even as they pass it along – can make flywheel-based systems more quickly responsive and more efficient than battery-dependent systems, not to mention more environmentally friendly, according to academic researchers. Fewer than 2 percent of datacenter installations use flywheels despite designs that make them more efficient not only by themselves, but also more efficient in the support systems required to keep them running, according to Bernie Woytek, of the architecture firm Gensler, which GM hired to design the datacenter. The flywheel "essentially eliminates a football field-sized room of batteries," that are temperature-sensitive and require their own cooling systems beyond that required by the servers and other datacenter hardware, Gensler said in a GM statement. The computing equipment also gets energy-conserving climate control in the form of in-row cooling systems, with blowers close to server racks to reduce the area to be cooled and energy required to get cold air to hot spots more quickly, and with less energy use than broader-based systems, according to GM. The system contains 432 server cabinets, 24 server clusters with six cooling units each and is able to process a collective total of more than a gigabit of data per second, according to a GM data sheet. The 5,040 square foot operations center to run it has 48 workstations, and 28 wall-mounted screens that display data use and operations on a video wall totaling 955 square feet. With the combination of in-row cooling and a flywheel to eliminate less efficient batteries, along with more HVAC to cool them, the Milford datacenter was able to cut its power use by 17 percent. Other systems – including a heat exchange that cools by circulating water outside into Michigan's relatively cool weather during three-quarters of the year – helped save a total of 70 percent from the energy demand of similar datacenters, Mott said. When the new datacenter design was proposed, GM expected it to save only 40 percent compared to the energy use of its other facilities, according to a 2011 GM announcement of the project. In May, GM began construction on an identical facility in Milford Mich. that will cost $100 million to build and $158 million for IT equipment. The two datacenters will mirror one another to provide data- and operations backup. Each facility is fed by separate utilities, using differing paths from power interchanges, and are in areas affected by different weather systems. The two are part of a company-wide consolidation, modernization and cost-saving makeover designed to make the whole company more power-efficient, environmentally friendly and quicker to change both its business and IT operations to meet new challenges, Mott said. Consolidating 23 datacenters into two is "part of an overarching strategy to transform not only information technology, but also allow GM's business operations to be more responsive to our customers, quicker to market and deliver on our objectives," he added. Image: General Motors
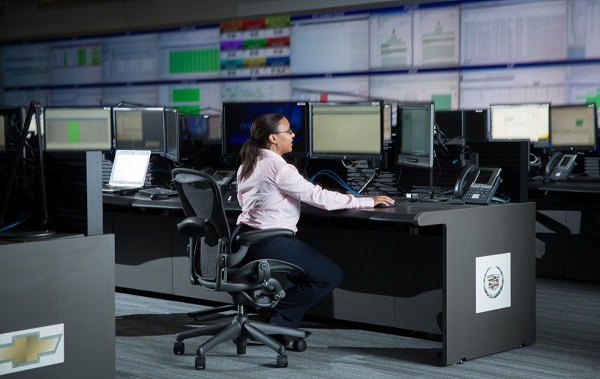